In our exploration of the IMPACT infrastructure articles, we’re delving into a fascinating case study concerning plinths – a crucial element that’s been revolutionized through the IMPACT software. Although the customer behind this groundbreaking innovation prefers to remain anonymous, their passion and pride for their work and product are unmistakable. With years of expertise in IMPACT and infrastructure projects, this customer is one of the select plinth producers in Sweden, offering exceptional quality precast elements to their clientele.
But what exactly are plinths, and why are they so vital?
Plinths are specialized precast concrete elements that serve as foundations in a wide array of construction projects, including warehouses, machine halls, industrial facilities, commercial buildings, riding stables, and more. These foundation units can be seamlessly combined with precast walls or longitudinal edge beams. Designed with precision, concrete plinths are engineered to bear the weight of a structure and can also provide support for the edge beams. Remarkably, the installation of edge beams is achieved without the need for any casting. Once the frame is in place, wall elements are introduced, marking a pivotal step in the construction process. For larger blocks, crane trucks or mobile cranes are employed to ensure the smooth assembly of these vital elements. This innovative approach has not only streamlined construction but has also enhanced the structural integrity of buildings, making it a remarkable advancement in the world of infrastructure.
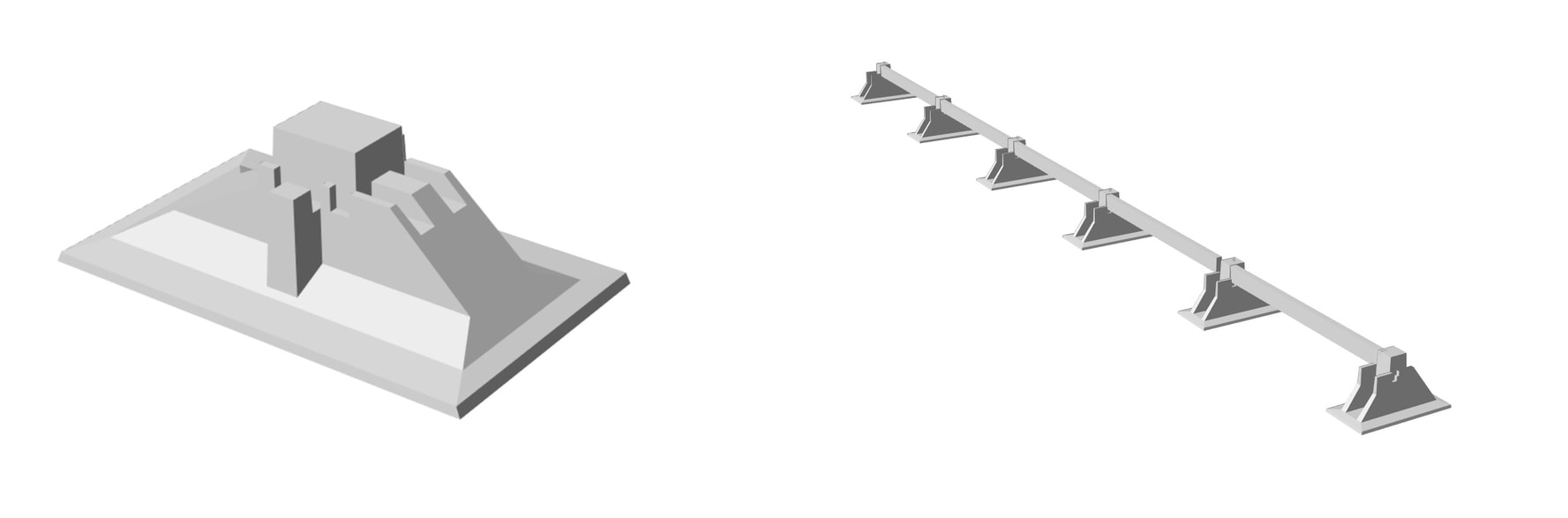
Pictures from © IMPACT Project Manager - Representation of plinths with & without edge beam.
How are Plinths designed and what is the IMPACT process?
The IMPACT process, can be summarized by the following graph
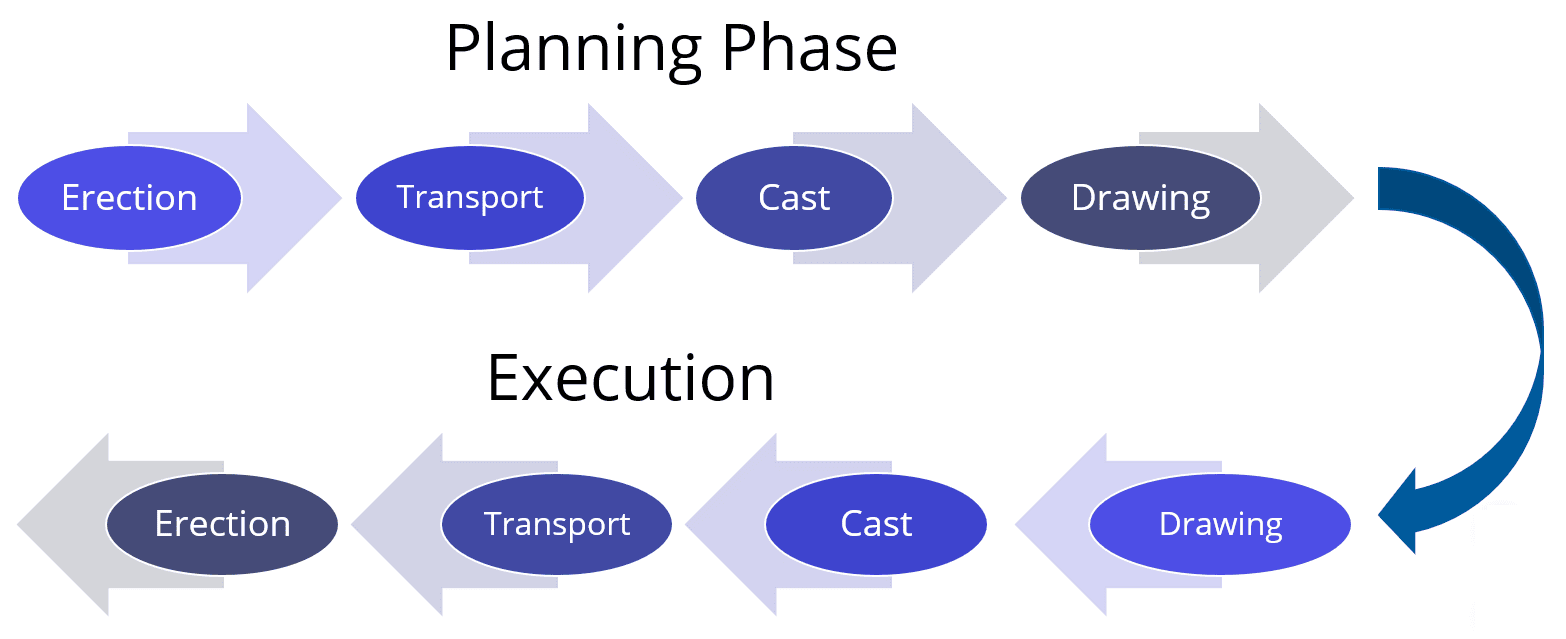
While the IMPACT process is an invaluable resource for plinth design, it’s important to note that there is no one-size-fits-all solution when it comes to designing specific elements. However, the flexibility and adaptability of the IMPACT process allow designers to integrate various design tools seamlessly.
For instance, you can utilize popular design software like Revit or AutoCAD 3D to create your plinth designs. Once your designs are ready, you can then import these elements into the IMPACT system, linking them to your project.
Now, here’s where the story takes an interesting turn. Some customers, like the one we’re discussing, opt for Tekla as their primary design and detailing tool. Tekla, known for its robust capabilities, offers a dedicated solution called IMPACT Tekla Base tools. This tool serves as a bridge between Tekla and IMPACT, enabling the smooth transition of your plinth elements into the production phase.
The synergy between Tekla and IMPACT Tekla Base tools is a game-changer. When Tekla is used for design and detailing, there’s virtually no excuse for your factory not to leverage IMPACT Production. This seamless integration results in a well-proven and blazingly fast workflow. It connects Tekla and IMPACT in great detail, ensuring that every aspect of your plinth design is transferred accurately.
What’s truly remarkable about this integration is the depth of information that gets imported into the IMPACT Database. This includes 3D geometry, properties, element marks, embedded items, reinforcement details, center of gravity (CoG), machine files, and even the statuses of the elements. The level of detail achieved through IMPACT Design and Tekla can be so closely aligned that it’s challenging to differentiate between the two, as evidenced in the following images:
Model representation in Tekla & Model representation in IMPACT Project Manager (only precast elements)
How are plinths produced in IMPACT
Plinths are a crucial component in precast production, and their creation within the IMPACT system is a fascinating process. What sets this apart is the seamless integration of the Carousel/Circulation plant with a specialized mold designed for plinths.
You might already be familiar with automated carousel systems, but what you might not know is that this system can be effortlessly implemented within IMPACT. In essence, you can design your pallets or tables to align with the position they occupy in the curing chamber. The maximum number of pallets corresponds to the curing chamber’s capacity, and the software connects directly to the production machinery, automating the entire process. Once you plan the elements, IMPACT for Cast updates in real-time, making it a brilliant solution for plants equipped with carousel systems.
Now, let’s delve into the production of plinths
The Plinth mold is designed to accommodate up to three plinths in a row, as depicted in the accompanying image.
While it may seem straightforward, creating plinths is a precise task with classified details that cannot be disclosed here. However, the software aspect is worth exploring. It’s essential to note that each type of plinth requires a specific-sized mold, and there are only a limited number of plinth types optimized for efficiency. To maximize production, ensure that the size of your pallets in IMPACT allows for only three elements per pallet.
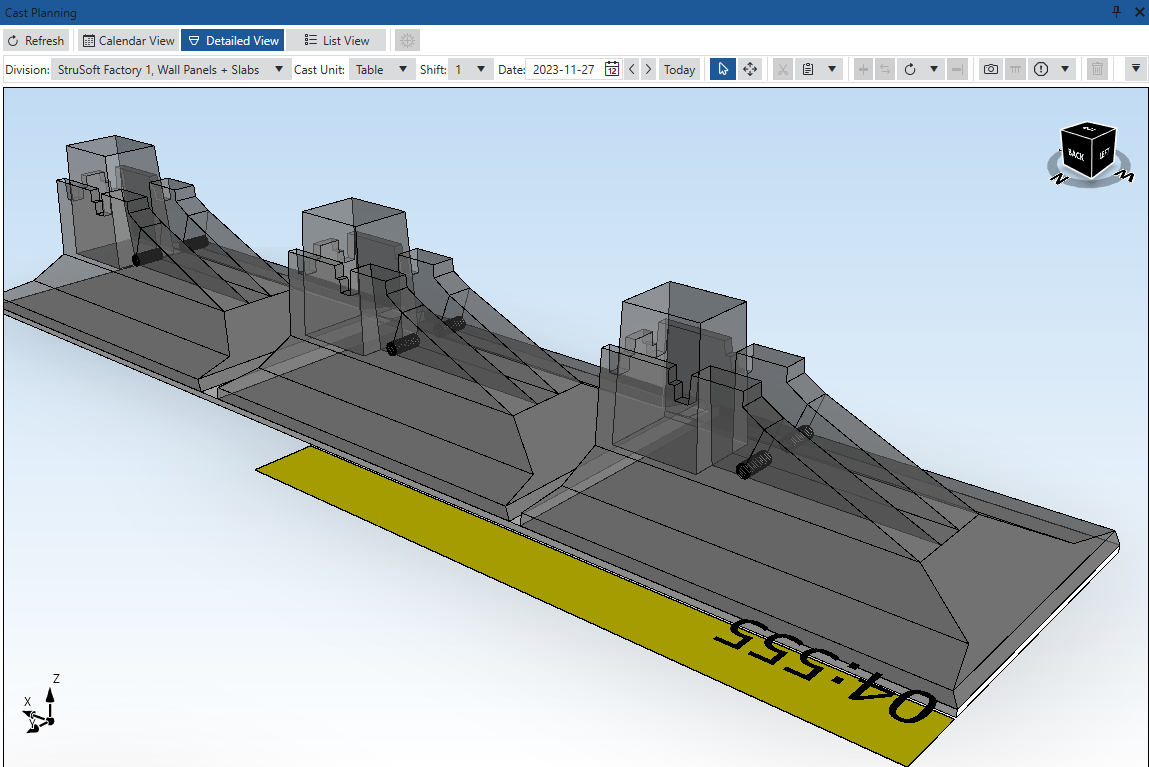
Picture from © IMPACT (3D Cast Planning of Plinths in IMPACT)
What about the transport or the stacking?
Regarding the transport and stacking of these plinths, the process is relatively straightforward, especially if you’re utilizing the IMPACT 3D Transport module. As shown in the image, elements are stacked and transported efficiently.
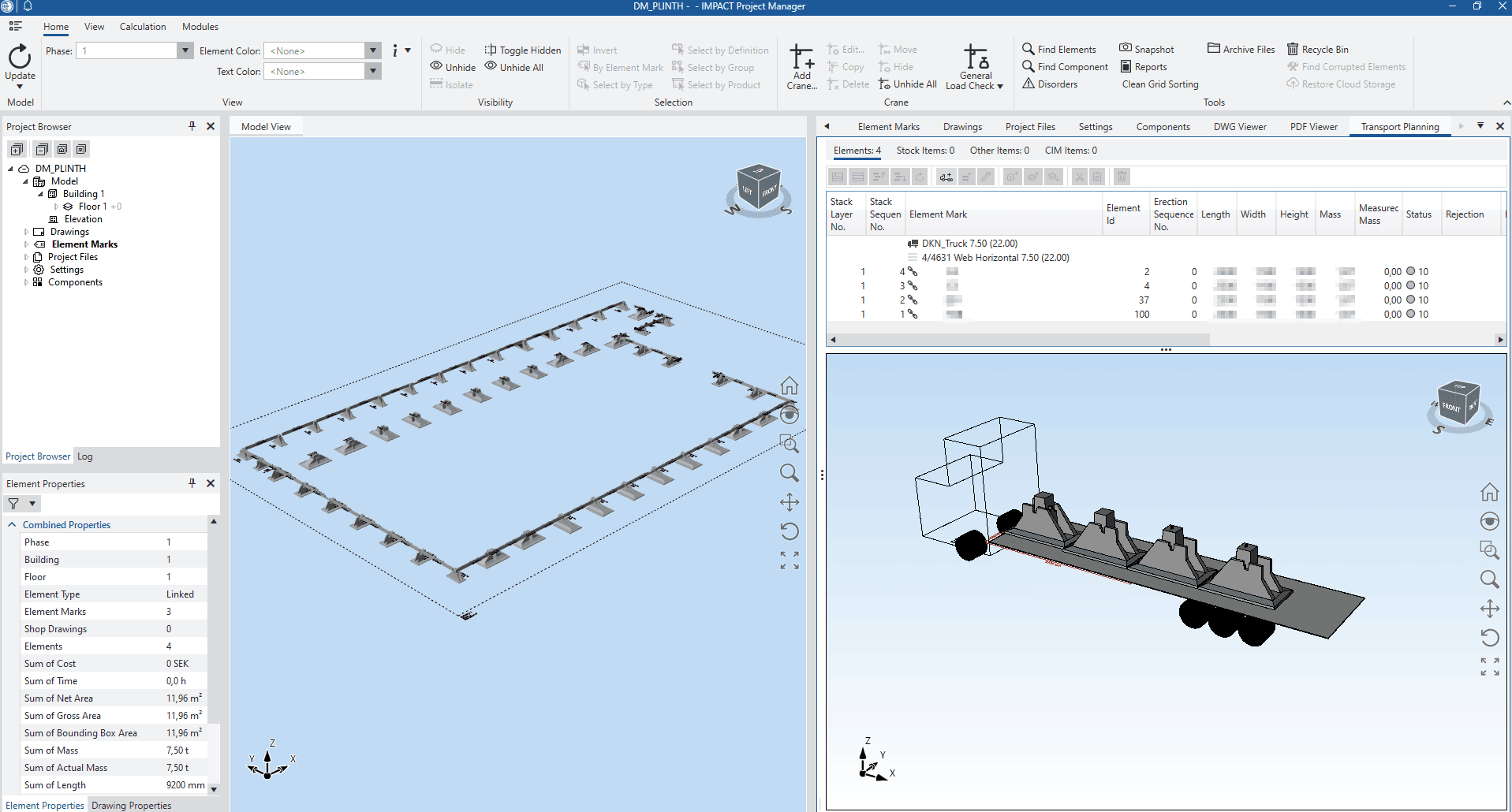
Picture from © IMPACT (3D Transport Planning of Plinths Elements)
All the pertinent data is meticulously stored in the database, and this information can be seamlessly integrated into other tools like IMPACT Cost Estimation or ERP software. This integration allows for cost calculations, the generation of Power BI graphs, deliverable checks, and much more. As a rule of thumb, the more data you have in your database, the better the output for your business.
In summary
When dealing with special types of elements in the precast process, various adjustments become necessary in the factory. However, with IMPACT Production, these adjustments are made easier due to the pre-defined processes, ensuring fewer errors in the factory and the delivery of high-quality precast products to your valued customers.
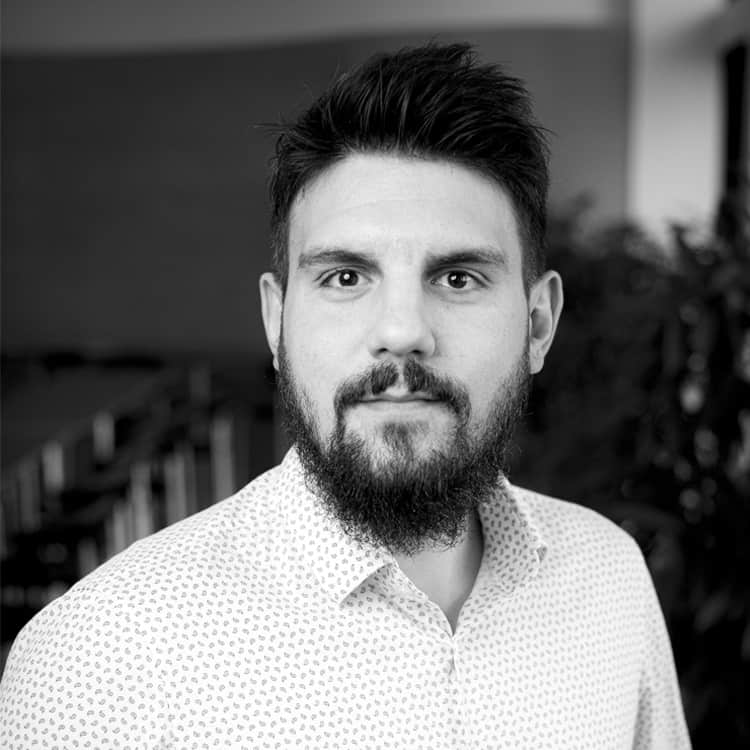
Thomas Gitsas
Would you like to learn more about IMPACT software and perhaps be interested in receiving a free demo and consultation on how we can support your Precast business? Then don’t hesitate to Book a 1:1 Teams meeting with Thomas – he will be happy to help you. Or you can follow the form below to Book a Demo.