Introduction
In the heart of Mälardalen in Nykvarn, approximately 1-hour south-west of Stockholm. AF Prefab stands as a testament to innovation and efficiency in the construction industry. During our recent visit to the factory, we had the opportunity to delve into the intricacies of their operations, guided by Factory Manager Dana Faidulla and Project Manager Anas Kuriya. One particular project, involving the casting of tunnel elements for ‘E4 Bypass Stockholm’, Sweden’s biggest road and tunnel project, showcased AF Prefab’s dedication to streamlining processes and overcoming challenges.
E4 – The Stockholm bypass – the biggest road and tunnel project in Stockholm, Sweden.
A 21 km motorway bypass is being constructed to relieve traffic in Stockholm: E4 Bypass Stockholm, or in Swedish “E4 Förbifart Stockholm”. The bypass, scheduled for completion by the year 2030, doesn’t just stand out as one of Sweden’s considerable infrastructure projects; its 18 kilometers of tunnel will make it world’s second-longest underground tunnel in city buildings. Stockholm is growing astonishingly fast – the Swedish capital has the fastest growth rate in Europe. The 14 islands that make up the Stockholm region are currently home to over a fifth of the Swedish population, with 2.1 million inhabitants. By 2030, this is expected to grow to around 2.5 million. For the region to continue to develop, well-functioning infrastructure is essential, and major investments are being made in Stockholm. For example, local public transport has been improved by a new railway through Stockholm’s central districts, the Citybanan, which was officially opened in 2017. Although the Citybanan represents an important step towards improving the public transport systems, it is not sufficient to combat the increasing car traffic in the city.
Stockholm currently only has one major road artery, Essingeleden. The road opened in 1967 and is designed for 80,000 vehicles per day. Fifty years later, it is traveled by around 160,000 on a typical working day – and rising. Consequently, the transport system in Stockholm is extremely vulnerable, with Essingeleden in particular very sensitive to road accidents. To address this situation, a 21 km motorway is being constructed that will link the south of the city (Skärholmen) with the north (Häggvik). The new road, “E4 Bypass Stockholm”, will divert traffic away from the city center to the west.
One of the longest road tunnels in the world
Most of the bypass – 18 of the 21 kilometers – will run through tunnels, making the bypass the world’s second-longest urban road tunnel, runner-up only to Tokyo’s Yamate Tunnel.
Pictures from © Trafikverket - The Swedish Transport Administration - E4 Förbifart Stockholm.
AF Prefab in Mälardalen supplies elements to AF Gruppen
During our recent visit, it was not only Dana Faidulla, Factory Manager at AF Prefab, that we met. We also met with Ann-Mari Beitdokken, Operations Manager at AF Gruppen, at E4 Forbifart Stockholm, or more specifically, in a rock tunnel close to the center of Stockholm. We had received permission from Ann-Mari and the AF Gruppen to visit below and see their work in the tunnel. Ann-Mari and Dana work closely together since AF Prefab in Mälardalen supplies approximately 13,000 elements to AF Gruppen in this 6 km twin-tube tunnel project.
In 2020, AF Gruppen was appointed contractor by Trafikverket, The Swedish Transport Administration. To build 6 km of the E4 Forbifart Stockholm, the E4 Stockholm Bypass is a 21 km new part of the E4 highway. It will mainly be built in rock tunnels close to the city of Stockholm. The works include a twin-tube 6 km tunnel and 7 km of ramp tunnels. Their contract includes roadworks and ventilation shafts.
The project started in the summer of 2020, and the the contract value is estimated at 3.400 MSEK.
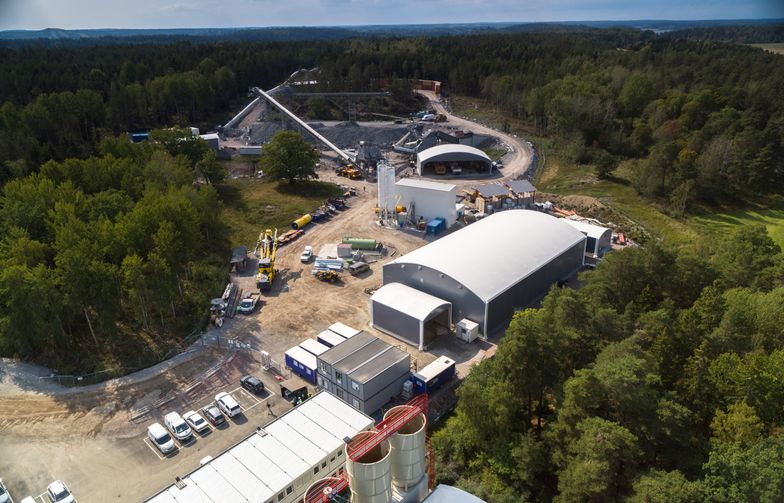
Picture from © AF Gruppen (AF Gruppen is appointed by Trafikverket)
Historical Context
AF Prefab’s journey began with a primary focus on casting poles for groundwork under the original company name, Pålplintar. Over time, they expanded their scope by venturing into casting wall elements for a tunnel project in 2017. However, this initial project encountered delays, leading to a prolonged delivery timeline. Fast forward to today, Factory Manager Dana Faidulla shared insights into the struggles faced during that project and the relief brought by the implementation of IMPACT in their current tunnel project.
Meet Factory Manager Dana Faidulla (To the left) and Project Manager Anas Kuriya at AF Prefab Mälardalen, a part of AF Gruppen Sweden
Current Project Overview
The groundwork for the ongoing tunnel project began in the spring of 2022, with the production of the elements kicking off in late October. The project contains around 13,000 precast components, categorized into two types: approximately 12000 standard elements and 1000 custom-made elements. The distinction is crucial as it dictates how to handle the production, storage, and transport.
Pictures from © Revit
Efficiency in Standard Element Production: The production of standard elements follows a meticulously planned process. AF Prefab’s factory floor is equipped with 11 flip tables dedicated to standard element production. Each day, these tables produce 22 identical elements, with a total of 9000 elements to be manufactured.
1. Reinforcement Cage Production: The reinforcement for standard elements involves two customized meshes from an external supplier. Workers assemble these meshes into reinforcement cages on factory tables, streamlining the process for subsequent use.
2. Jig Implementation: To save time, permanent jigs are placed in the bottom of the mould for the two recesses needed for each element.
3. Lifter Placement: The lifters, always in the same position for standard elements, are efficiently placed in the mould through pre-designed recesses.
4. Storage: Customized A-frames store over 150 standard elements each, with a total of around 5000 elements currently in the yard.
5. Transport: A customized lifting device on wheel loaders facilitates the movement of elements from the hall to storage and from storage to transport.
6. Loading for Transport: Cassettes loaded with 5 elements each are transported to the tunnel, and empty ones are collected on the return journey.
Special Element Production
The production of special elements mirrors residential building processes, with customizations in formwork for efficiency.
Storage Strategy
To combat color changes due to weather conditions during prolonged storage, AF Prefab employs a ‘first casted-first delivered’ strategy. This ensures uniform storage times for each standard element, mitigating color discrepancies.
Logistics, Assembly, and Erection
With a one-week notice, preparations for assembly are facilitated by utilizing available space in the tunnel communication between Dana and Ann-Mari for stack storage. The stacks are strategically placed in predetermined locations, streamlining the assembly process by eliminating the need for the erection team to relocate elements during the process; ensuring they are precisely positioned from the outset. The erection process involves the use of vacuum technology, suspending the elements rather than having them stand on the ground.
Element Control System
Element Control System Ensuring efficient control over a multitude of elements necessitates a robust system. The abundance of controls is seamlessly managed by storing them systematically. Controls produced in the factory can be conveniently accessed and monitored from any location, including the tunnel construction site.
IMPACT Integration
AF Prefab has been utilizing IMPACT for cast, transport, and element controls for almost three years, and since the beginning of 2023 they have also been using IMPACT for the tunnel project. Dana Faidulla emphasized the significant benefits, noting that IMPACT has alleviated numerous challenges compared to their previous tunnel project.
AF Prefab’s approach to the tunnel element production project showcases an inspiring case study in efficiency and adaptability. Through strategic planning, customized processes, and the integration of IMPACT Precast, they have not only overcome past challenges but set a benchmark for future endeavors in the construction industry.
“Before we started with Lovön, we produced tunnel walls for one of the other stretches of förbifarten. With the implementation of IMPACT, the production of this stretch has been significantly more organized and has required fewer people to coordinate the production and transportation process. Also, being able to conduct the controls via the software and having them stored on impact will improve the longevity of our project.”
Pictures from © IMPACT Project Manager - On-site at AF Prefab Mälardalen
A huge thank you to Dana Faidulla for his hospitality and generosity – and thanks for spending two days together with us, first at Stockholm’s new bypass and second on-site at AF Prefab in Mälardalen. We are very grateful for this cooperation and trust!
And a huge thanks to Ann-Mari Beitdokken, Operations Manager at AF Gruppen, for letting us visit the tunnel exceptionally. AF Gruppen is building a part of the E4 Bypass Stockholm for the Swedish Transport Administration. You can read more about it here.
The article was written by Mathias Hansen – in collaboration with Linus Karlsson and Dana Faidulla.
Would you like to learn more about IMPACT software and perhaps be interested in receiving a free demo and consultation on how we can support your Precast business? Then don’t hesitate to Book a 1:1 Teams meeting with us – we will be happy to help you. Or you can follow the form below to Book a Demo.